Find the right solution for your business with our free Fleet Management Buyer’s Guide.
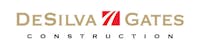
DeSilva Gates Construction locates their assets and big savings
In searching for their assets, a construction company uncovers big savings
When you've been in business for more than 80 years you'd think there wasn't much new to learn. Construction company DeSilva Gates has shown that you're never too old to master the newest tricks.
Started in 1932 and based in Dublin, California, DeSilva Gates has utilized new mobile enterprise management (MEM) software to improve efficiency, saving time locating equipment and scheduling maintenance.
Rich Poppoff, Equipment Superintendent at DeSilva Gates explains the "hide and seek" struggle the company was dealing with.
"We had a general idea where an asset was. Problem was that we'd go out there and couldn't find it so we would end up renting a piece of equipment instead."
"Verizon Connect has allowed us to accurately pinpoint where an asset is and not wander around looking for it."
Locating assets quickly has proved to be a major cost-saver in more ways than one.
Breakdowns can cost up to $20,000 an hour, so delays in getting assets fixed can represent a major hit to the bottom line. With accurate location information and commercial navigation solutions, runners are delivering replacement parts faster than ever before, meaning equipment is up and running again much sooner.
Reduced over-maintenance: Saving dollars, saving the environment
DeSilva Gates is not just saving money by reducing downtime; they've also eliminated unnecessary servicing, switching from standard intervals to using engine data to only service when the equipment actually needs it.
One example is the drain interval on their pickup trucks, which used to be the industry standard of 3,000 miles. With actual engine data, they can minimize waste.
"Now that we're tracking the life expectancy of our oil, we've extended the oil change on a lot of our vehicles to eight or 10,000 miles."
Management is also making better, faster decisions about reported defects. Electronic inspections (including paperless DVIRs) have significantly improved the speed at which defects are managed and resolved.
"Vehicle inspection reports were three days old by the time we were getting them. Now with real-time data, we get an alert that lets us know someone has checked a box to say 'hey I have this condition' and we get to make the choice about whether it's an out of service condition or whether it's something that can wait until the next scheduled service."
The data's changing how we drive
Unsafe driving habits used to go unnoticed but sharing the data with drivers directly through the Verizon Connect Coach app has yielded some surprising results.
"Once we started sharing that with all the employees we noticed a marked drop in the occurrence of people speeding.'
Jeff Workman, Safety Director, DeSilva Gates
"Verizon Connect has given us a clear window into driver behavior," notes Jeff Workman, Safety Director at DeSilva Gates. "We're actually able to describe to someone, look at the number of rough starts … the number of times you were over seventy miles [per hour].''
DeSilva Gates also use Verizon Connect Coach, a scorecarding solution that uses gamification, to reward and motivate drivers for meeting their safety goals.
"It's a really strong motivation for people to improve their driving behavior."
Find out how our platform gives you the visibility you need to get more done.